Mechanical contractors work on a wide range of complex and high-stakes projects, including data centers, semiconductor plants, hospitals, and more. These projects demand precision, efficiency, and the ability to deliver on tight deadlines. In a competitive market where the pressure to improve lead times and margins is growing, contractors are also facing a significant shortage of skilled labor. The Spool Welding Robot (SWR™) is designed to help mechanical contractors overcome these challenges by dramatically increasing pipe welding productivity and ensuring consistent, high-quality welds.
The Spool Welding Robot for Building Construction
Suggested Solutions
Welding Process
Pipe Materials
Industry Codes
Meeting the Needs of Mechanical Contractors
The SWR™ is designed to meet the specific needs of mechanical contracting. Whether it’s projects involving critical infrastructure like hospitals or advanced technology facilities like semiconductor plants, precision and reliability are essential. The SWR™ delivers on these needs by automating the welding process, which not only helps to overcome the shortage of skilled welders but also ensures that every joint in piping meets the highest industry standards, such as those required for ASME B31.1 and ASME B31.3 compliance.
Increasing Productivity and Competitiveness
In an industry where competition for prefabrication is intensifying, the SWR™ offers a significant competitive edge. Over the past 15 years, prefabrication has grown from 15-20%, with shops increasingly looking for ways to capture more market share. The SWR™ enables mechanical contractors to increase their pipe welding productivity by 3-5 times for carbon steel pipes, achieving 200-350 diameter inches per shift. For stainless steel pipes, the productivity boost can be as high as 12 times, with 569-998 diameter inches per shift. This significant increase in productivity allows contractors to complete projects faster, lower costs, and improve delivery timelines, helping them to win more projects and increase margins on those they have already secured.
Reducing Repair Rates and Costs
Welding defects and the need for repairs can be costly and time-consuming, with repair costs typically ranging between $800-$1,000 per weld. The SWR™ addresses this issue by significantly lowering repair rates to less than 1%, compared to the industry average of 3-5%. For example, a fabrication shop producing 6,000 welds per year could save up to $180,000 annually by reducing repair rates. This reduction in repairs not only improves the bottom line but also enhances the reliability and quality of the final product, ensuring the structural integrity of critical systems.
Flexibility and Integration
The SWR™ offers flexibility for various welding tasks, including the ability to weld slip-on flanges with the SWR-F option. This flexibility is crucial for mechanical contractors who need to adapt to different project requirements. Additionally, the SWR™ integrates seamlessly with STRATUS and PypeServer, further streamlining the construction process. This integration enables contractors to optimize their fabrication workflows, reduce lead times, and maintain a high level of precision throughout the project lifecycle.
Combatting the Skilled Labor Shortage
The mechanical contracting industry is facing a welder shortage crisis, with the average age of welders in the United States being 55 years old and a predicted shortage of 314,000 welders by 2024. The SWR™ helps to mitigate this issue by working with less experienced operators to produce high-quality welds consistently. As a collaborative robot (cobot), the SWR™ enhances shop productivity and allows contractors to maintain high standards even with a limited pool of skilled labor.
Case Studies
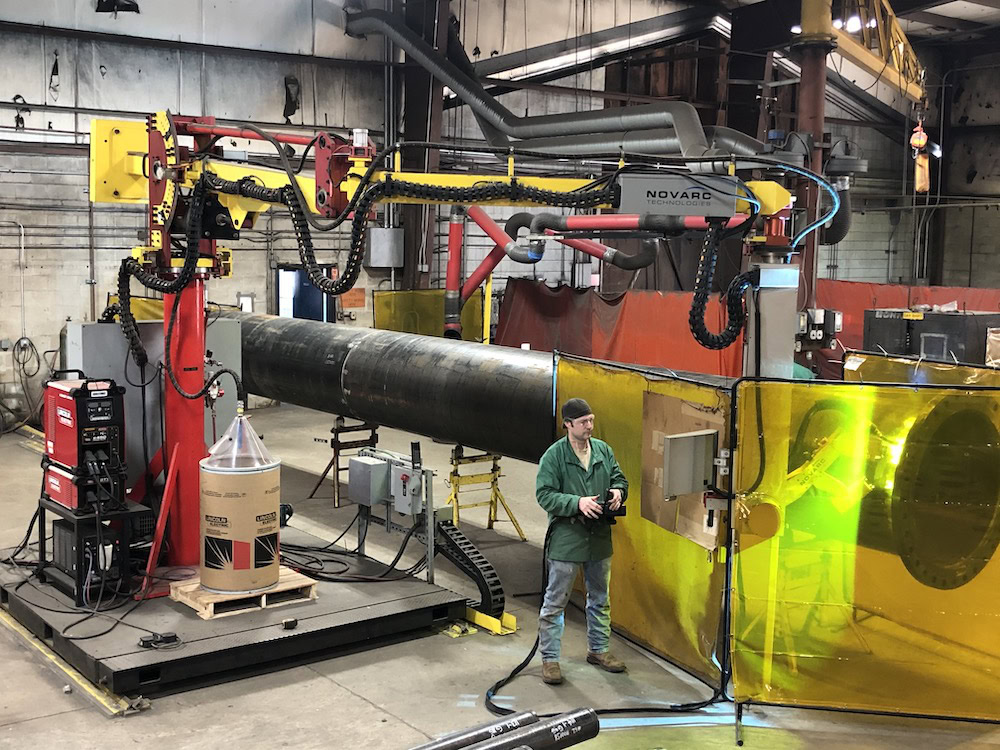
By implementing Novarc’s solution, W.W. GAY Mechanical Contractor Inc. has been able to achieve over 200% increase in shop productivity, 100% Radiography Test (RT), and on some projects a 12x increase in pipe welding productivity.
View Full Case Study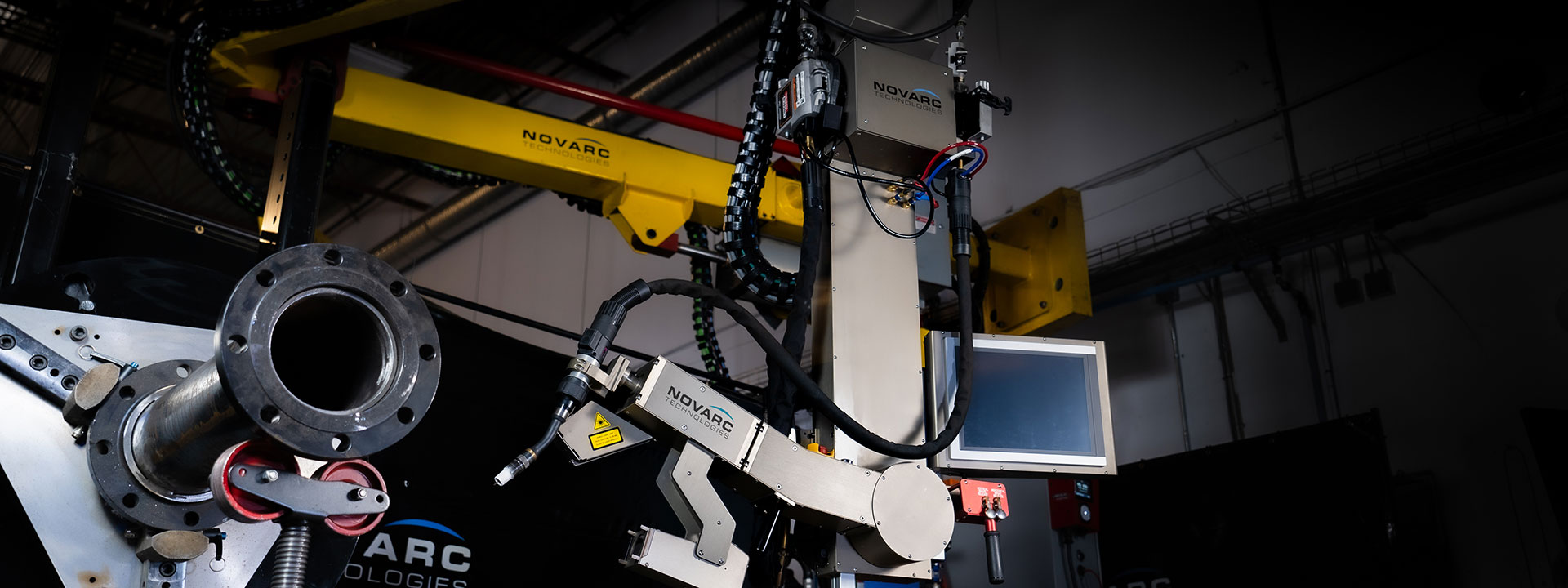
ColonialWebb
ColonialWebb Contractors Inc. Scales New Heights with Novarc's Spool Welding Robot, Transforming Their Welding CapabilitiesView Full Case Study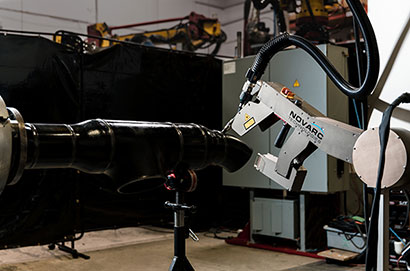
Harder Mechanical Contractors
Harder Mechanical Tackles Welder Shortage with Novarc's Spool Welding RobotView Full Case Study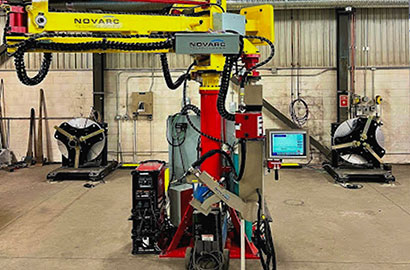
Kleeberg
Kleeberg Boosts Welding Efficiency and Consistency with Novarc's Spool Welding RobotView Full Case Study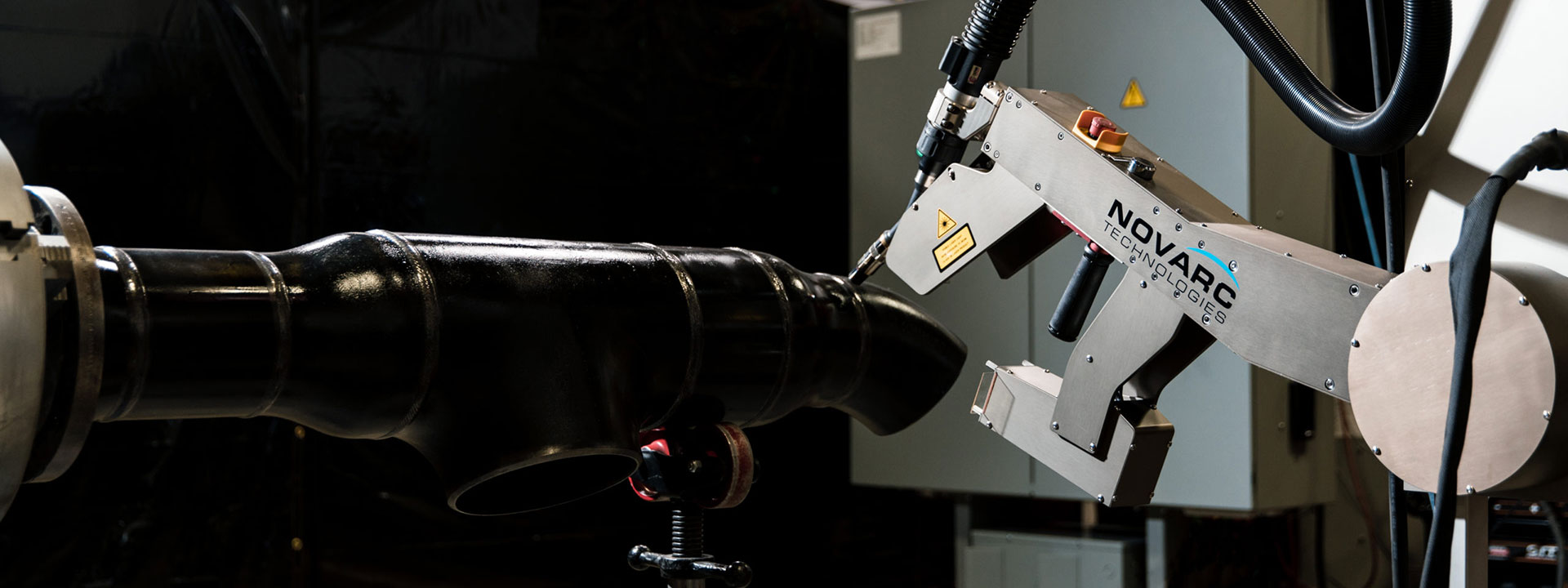
Metropolitan Mechanical Contractors
MMC Enhances Welding Quality and Efficiency with Novarc's Spool Welding RobotView Full Case Study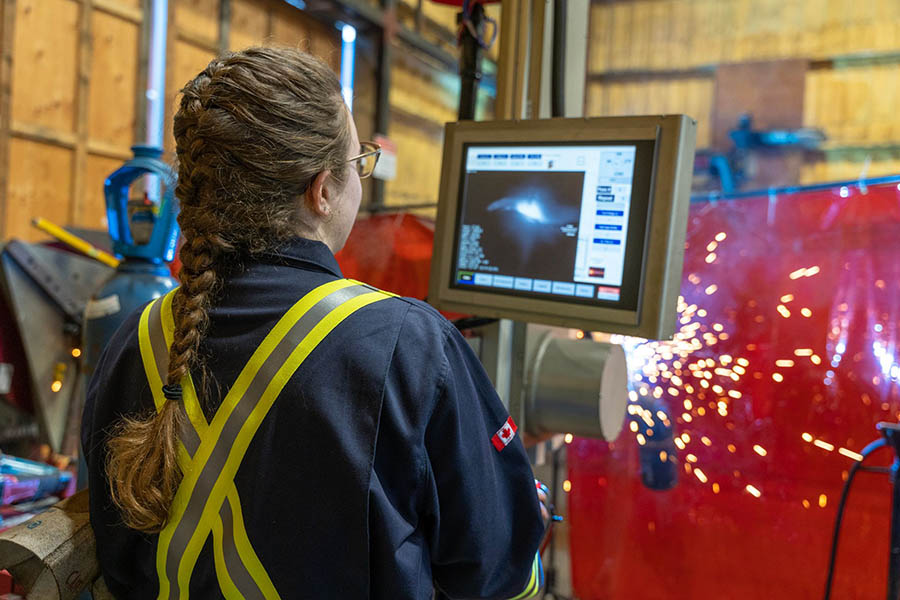
Pitt Meadows Plumbing & Mechanical Systems
Pitt Meadows Plumbing Boosts Productivity and Quality with Novarc's Spool Welding RobotView Full Case Study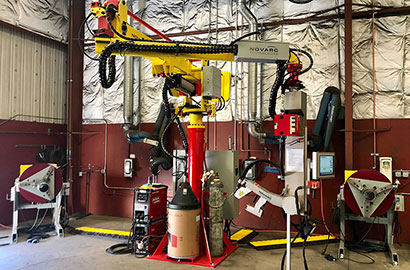