Challenges that Forced them to Investigate New Solutions
Cord approached Novarc because they were trying to adapt to the new technological changes in the industry and get ahead of their competition. “We’ve been using a lot of the same construction methods for a while, so it was a way for us to step into the next evolution of welding. We were at a stage where we had maximized efficiencies, but weren’t exactly getting ahead either”, says Jamie, Project Manager at Cord.
They also looked into robotics to prepare for the shortage of apprentices that the industry will be facing. “Where we struggle in the industry as a whole right now is the number of apprentices; there are not a lot of new workers going into the trades. In 5-10 years, this labor shortage will really impact the industry. A lot of the welders currently employed are getting older and retiring. It’s a good opportunity to get into the robotics”, says Jamie.
Novarc's Spool Welding Robot (SWR) Solution
With the smallest footprint in the industry, the Spool Welding Robot (SWR) is a collaborative welding machine designed specifically for 1G welding. Companies that have invested in the SWR have increased their pipe welding productivity by 2 to 3 times, depending on the material grade, size and thickness, and have dropped their repair rate to less than 1%. These massive gains are making our customers more competitive when bidding on jobs, and it has increased margins on contracts they’ve already won. The SWR allows our customers to bid on projects that they never would’ve considered before because now they can predictably execute on short delivery timeframes.
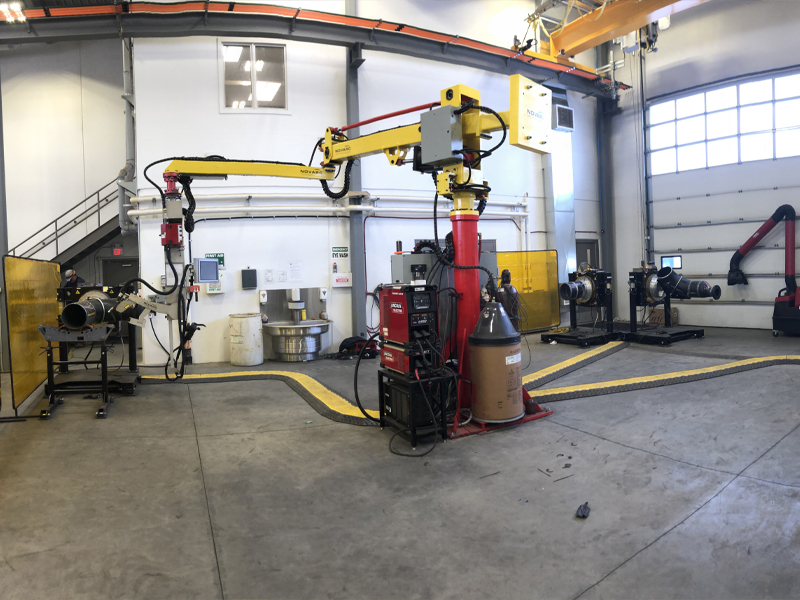
“Novarc was the first one we reached out to. We did look at a few other options, but in regards to what we build, Novarc seemed like the most logical, because of the basic setup. Novarc uses a lot of common industry parts, that are readily accessible. Their competition in this market use more complex components, and therefore, repairs could lead to several weeks of down time”, says Jamie.
Cord has achieved up to 35% savings in bid rates, and a 230% increase in pipe welding productivity since implementing the SWR. With these measurable results, Cord has increased their investment in SWRs with the recent purchase of their fourth and fifth machines.

Increase in Pipe Welding Productivity

Up to 35% Savings in Bid Rates
The Use of the Spool Welding Robot (SWR) in a Recent Project
Cord has recently used the SWR in one of their recent projects, which included a total of 220K Factored Diameter Inches (FDI) of pipe fabrication.
“We were able to increase efficiencies on the project with Novarc’s Spool Welding Robot. We were very impressed with the ability to maximize productivity, while providing a quality product to our client”, says Jamie. “For example in the case of a 24” XH (0.5” pipe thickness) weld, Novarc’s Spool Welding Robot outperformed our welders by 3 times!”, says Jamie.
“Being almost two years into this and expanding, we are on the right track. We will see some big things happening in the next year, so I’m pretty excited myself. We’re moving into a new shop, and we’re going to be more efficient with how we operate. Novarc’s Spool Welding Robot has encouraged us to implement more technology”, says Jamie.
